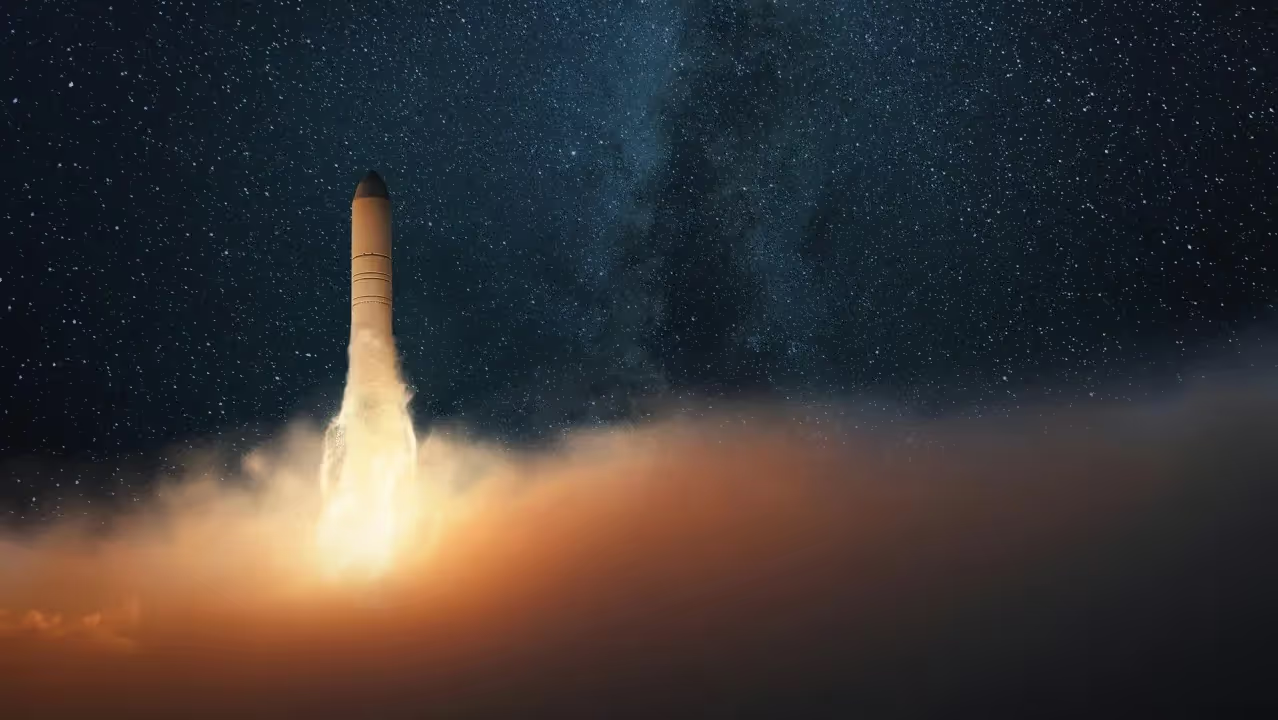
Optimized rocket fuel is key to mission success
Rockets rely on various combinations of fuel and oxidizers to generate the tremendous power needed to overcome Earth’s gravity. Oxidizers and fuels are stable elements at room temperature, but when mixed and triggered by a heat source, they create an explosive reaction that provides the rocket’s thrust.
By adjusting the ratio of fuel to oxidizer, engineers can control various aspects of the rocket’s performance. Each combination provides a unique set of characteristics, benefits, and drawbacks, impacting performance measures like thrust efficiency, as well as other considerations such as toxicity, cost, and safety. As such, choosing the best propellant package for each voyage is a critical decision that depends on many variables related to the rocket’s mission.
Gaseous propellants, for example, are impractical for most long-distance rockets because of the large volume that would be required, but compressing and cooling these substances into their corresponding liquid phases provides an optimal volume-to-power ratio for large-scale rocket applications. Some propellants, however, have extremely low boiling points and require cryogenic cooling at temperatures below –150 °C (–238 °F) to liquefy. That can be a significant drawback to using these fuels for rocket propulsion, so the benefits must outweigh the costs and challenges of this requirement for a specific mission to justify their selection.
Two important performance characteristics of propellants, which are sometimes confused, are thrust and specific impulse. Thrust measures the propellant’s reaction force potential, or the amount of weight the rocket will be able to lift. Specific impulse (Isp) defines how efficiently a propellant can convert its mass into thrust, based on the time that a certain quantity of propellant can push a load. Engines using propellants with a high specific impulse tend to have lower thrust but use their propellant’s mass more efficiently. In short, they get greater gas mileage.
Table 1 compares the key properties of common rocket fuel packages. The RS-25 engine employed by NASA’s Artemis Space Launch System (SLS) rocket uses the LOX/LH2 propellant package. However, rockets being developed by some commercial organizations, including SpaceX’s Raptor and Blue Origin’s BE-4, are powered by the Liquid Methane/LOX package.
Among modern rocket propellants, LOX/LH2 exhibits the highest Isp value. That efficiency and a track record of reliability are the primary reasons why the LOX/LH2 package has been commonly used as a rocket propellant for the last five decades, in spite of both atoms requiring cryogenic cooling. Also, while other propellants release large quantities of polluting chemicals and greenhouse gases after combustion, the primary by-product produced by the combustion of LOX/LH2 is water, making it a more sustainable fuel.
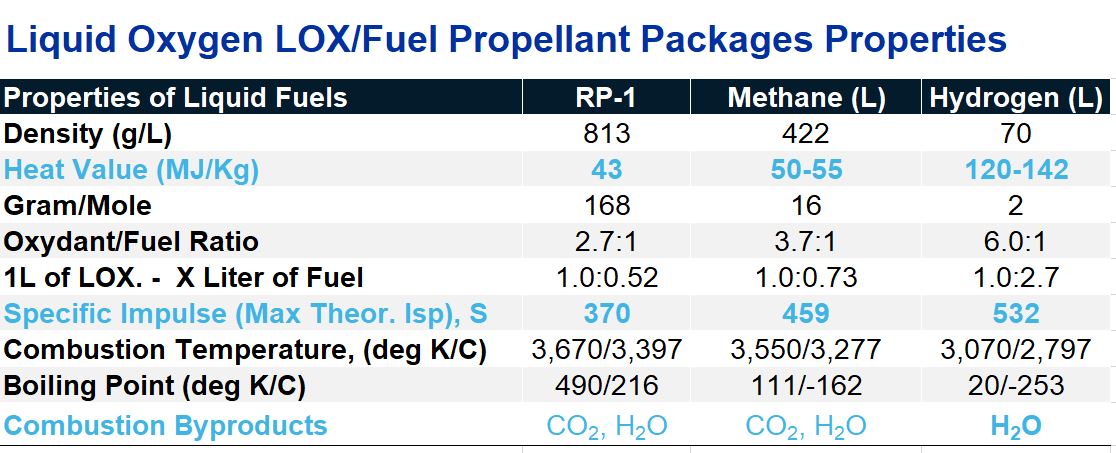
Note: *RP-1 (Rocket Propellant-1) is a highly refined form of kerosene and is widely used in liquid rocket engines (i.e., the Saturn V rocket engine).
Radical reaction chemistry of LOX/LH2 rockets
Hydrogen and oxygen are stable elements that will not spontaneously react when mixed at room temperature. For a reaction to occur, H–H and O=O covalent bonds need to be broken. When enough energy is supplied to overcome the H–H and O=O bonding energy, a chain reaction will occur until water is formed. This reaction toward water’s stable structure releases large amounts of energy during H2 combustion with O2.
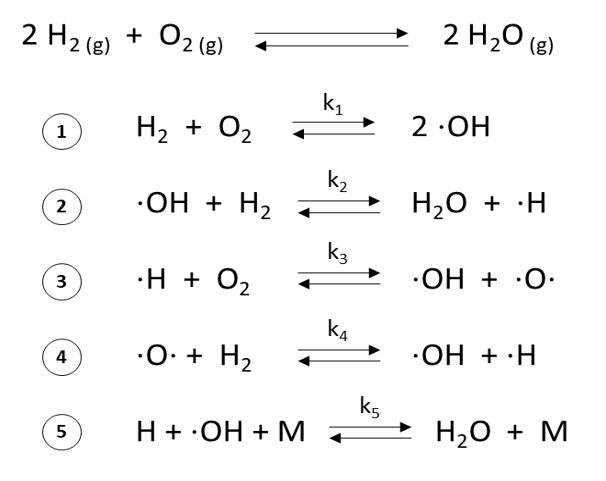
Despite this reaction’s apparent simplicity, H2 combustion with O2 is complex and involves several intermediary reactions with H and O radicals. The main reactions leading to the formation of water are listed in Figure 1. Chain-branching reactions occur when one radical generates two or more radicals (Figure 1, reactions 3 and 4). Because these reactions produce more reactive radicals than they consume, they accelerate, explaining the explosive nature of the reaction.
These radical reactions don’t always happen in the exact order displayed in Figure 1, and other radicals not mentioned here may be formed through other chain reaction schemes. Propellant mixture, pressure, and temperature also influence H2 combustion kinetic mechanisms.
Advancing engine design to power Artemis
In addition to fuel optimization, rocket engine design is equally critical to maximizing the power of modern rockets. Today’s rocket engine designs leverage foundational innovations developed during Germany’s World War II V-2 rocket program. The availability of new materials and other technological innovations have allowed engineers to advance these designs to increase the power, durability, reliability, and efficiency needed to power modern space missions.
Designed in the 1970s by Aerojet Rocketdyne, the RS-25 engine was originally developed and used for NASA Space Shuttle missions. Five generations of innovation later, the RS-25s that power Artemis’ SLS rocket are sophisticated cryogenic engines that incorporate decades of technology advancements and design optimizations, making them some of the most efficient and powerful rocket engines ever produced.
To create a powerful and consistent thrust, rocket engines need to be fed with a large volume of high-velocity liquid propellant via the turbopump. The first version of the turbopump (Figure 2) was developed by V-2 engineers in the 1940s. It was revolutionary in its design and performance, with one steam turbine rotating at 4,000 rpm to drive centrifugal pumps for both the fuel and oxidizer. More than 60 years later, the modern turbopump is still one of the most critical and complex components responsible for the performance of modern rocket engines.
U.S. Manned Rocket Propulsion Evolution
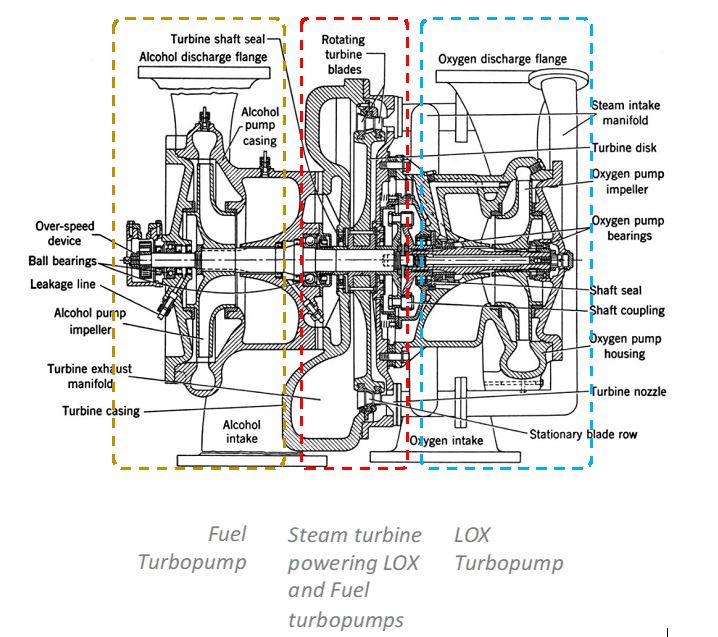
The RS-25 engines in the Artemis rocket utilize the LOX/LH2 cryogenic propellant package based on its superior specific impulse. However, a significant difference between the densities and flow rates of LH2 and LOX prevents the RS-25 from operating on a single turbopump. Hydrogen’s density is extremely low (71 g/L), which means that it will take 2.7 times as much LH2 to proportionally match the LOX quantity for efficient combustion to happen. To accommodate these very different cryogenic liquids and their physical properties the RS-25 uses two separate turbopumps.
These modern high-pressure turbopumps are feats of engineering. Their turbines contain dozens of blades that are only the size of a quarter. Rotating between 28,000 and 35,000 rpm, each blade provides more power than a Corvette engine, allowing these turbopumps to generate tens of thousands of horsepower.
Space aspirations driving innovation across industries
Rocket fuel and engine technologies are obvious areas of innovation driven by the space program. However, the current focus on returning humans to the moon and eventually reaching Mars also serves as a catalyst to accelerate new research across a wide range of industries including medicine, material science, communications, electronics, and even agriculture. Many of these innovations, in addition to enabling space missions, result in improvements to products that benefit all of us here on Earth as well.
Interested in other new technologies being developed for the Artemis mission? Read more about innovations in food science that will nourish astronauts heading to the moon and beyond.