
With nearly 210 gigawatts of installed capacity, solar energy is now a fixture of the U.S. energy landscape. Solar accounted for 67% of new electricity-generating capacity in the U.S. in the first half of 2024. Globally, solar generation has reached close to 1300 terawatt hours.
This is an unequivocal benefit for the planet and emissions-reduction efforts, but the maturation of the solar panel industry also brings new questions, specifically what to do with all those photovoltaic (PV) panels once they reach their end of life (EOL). In fact, the first generation of PV panels, installed in the 1990s, are now reaching their EOL since solar panels have an approximate 30-year lifespan. With the amount of PVs being installed today, it’s possible that the world will be handling 78 million tons of PV panel waste by 2050.
PV waste presents many challenges, namely, how to recycle and reclaim valuable materials. In the absence of dedicated recycling programs, components in solar panels will end up in landfills, polluting the environment, which is at odds with the reason behind their widespread use.
These challenges also offer extensive opportunities for more circular energy solutions, more readily available raw materials to make new panels, and greater compliance with changing government regulations. Our analysis of the CAS Content CollectionTM, the largest human-curated repository of published scientific information, reveals where PV EOL research is headed and how we may find a more sustainable path forward.
Are solar panels recyclable?
The short answer is, yes, and there are three current methods to do so. Typical PVs consist of a silicon wafer along with silver, lead, copper, and tin interconnects that are usually encapsulated in poly(ethylene vinyl acetate) (EVA) on both sides (see Figure 1). Of all the components, silver is the most valuable. It accounts for less than 1% of a PV’s mass, yet it’s worth 47% of all reclaimed materials.
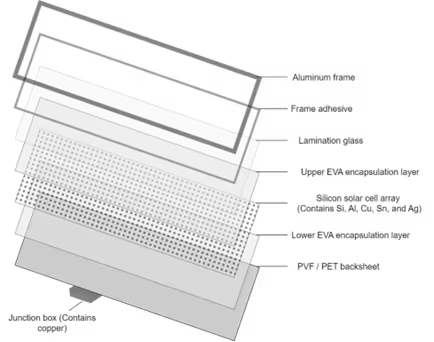
Current recycling processes involve four steps:
- Dismantling the aluminum frame, copper cable, and junction boxes
- Removal of the glass layer
- Removal of the polymer encapsulant
- Recovery of silicon and metals
The most challenging process is the removal of the glass layer, which is usually pasted to the encapsulated solar cell using adhesives, also called delamination (see Figure 2).
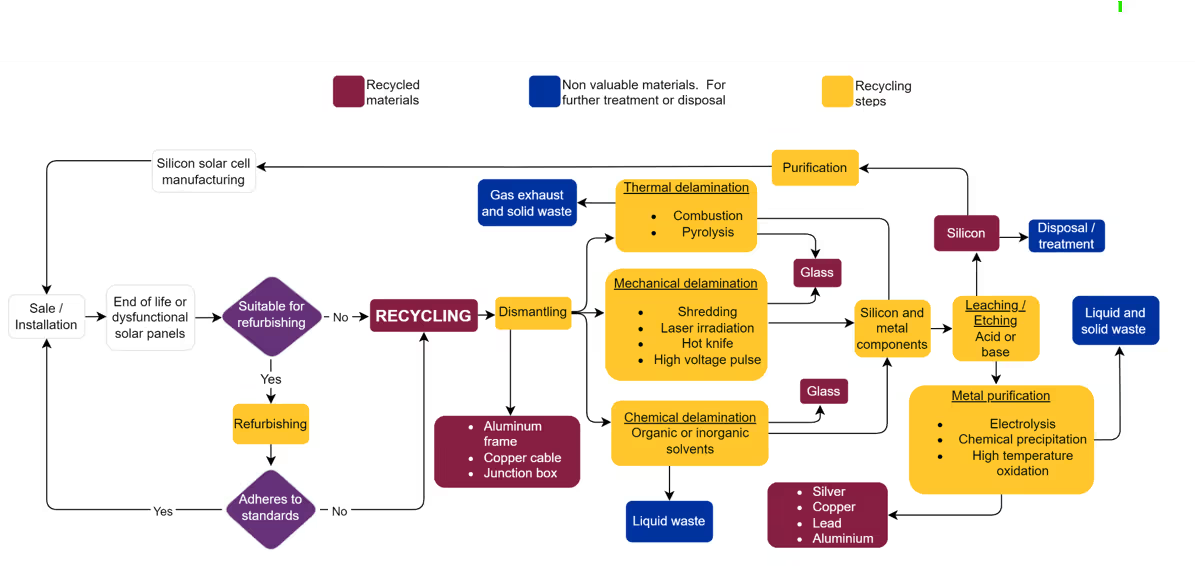
The three current methods for solar panel recycling all involve benefits and tradeoffs (see Figure 3):
- Thermal delamination: In this process, PVs are subject to pyrolysis at temperatures ranging from 300-650 °C. This leads to the separation of the glass and decomposition of the adhesives. This is the most cost-effective and the common type of PV recycling, but due to its high operating temperatures, thermal delamination requires more energy, which leads to toxic fume emission.
- Chemical delamination: This recycling method is effective without damaging the glass and solar cells. However, the organic solvents and inorganic acids or bases used in this process require extended time to react with the adhesives and encapsulants, lengthening the processing time up to 10 days. The chemicals used in this process are also expensive, and the used chemical waste requires a complex treatment process.
- Mechanical delamination: This consists of shredding the dismantled solar panels, followed by milling and separation. Though mechanical delamination is the simplest of the three processes, removal of the encapsulant polymer is inefficient.
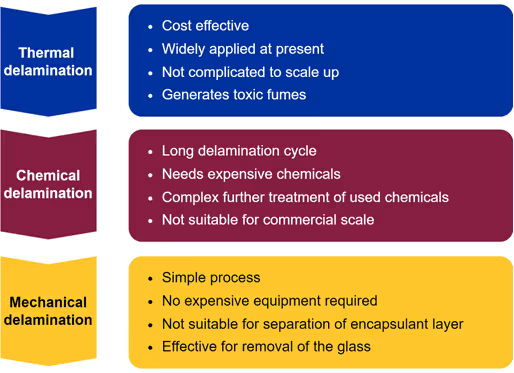
Challenges in solar panel recycling
Since there are benefits and drawbacks to all PV recycling methods, researchers are looking for ways to improve them. Our analysis of the current research landscape reveals that patent publications are most common, demonstrating the extensive commercial interest in these processes (see Figure 4).
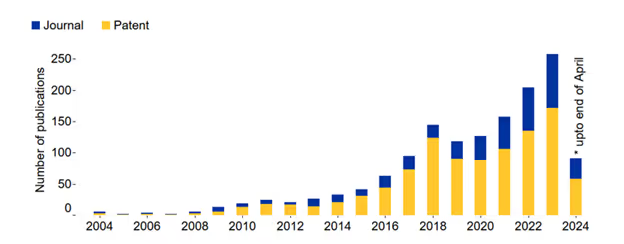
When we look closer, we find that concepts related to thermal delamination, such as heat treatment, thermal decomposition, heating, and calcination, are the most indexed (see Figure 5).
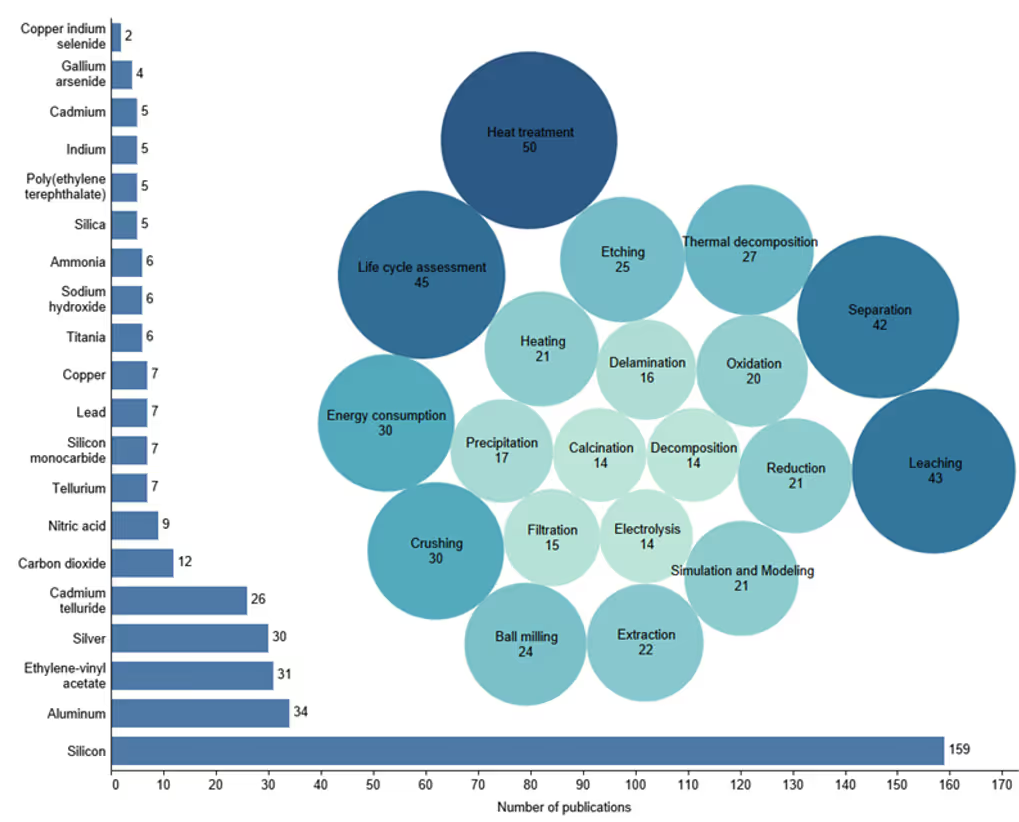
However, many challenges must be overcome to successfully scale up PV recycling to handle the influx of panels reaching their EOL. As mentioned, emission of toxic fumes and disposal of hazardous chemicals complicate current recycling processes. Another issue is that the recovered silicon is typically contaminated with other elements and cannot be used in new solar panels. To reuse the silicon in the wafer manufacturing process, it must be refined to achieve high purity, which ranges from 6N (99.9999% pure) to 11N.
It’s critical that PV manufacturers can reuse silicon because the silicon manufacturing process is responsible for more than half of the energy used in PV production. Further complicating this process is the fact that silicon wafers made 30 years ago aren’t as high-quality as those made today.
Lastly, there is uncertainty around the cost-effectiveness of PV recycling. A recent study found that recycled materials were much cheaper than virgin materials: those virgin materials for a PV were calculated at 90 USD/m2 whereas recycled materials recovered via the full recovery end of life photovoltaic project (FRELP) cost just 12.43 USD/m2. That cost drops even lower, to 1.19 USD/m2, when the environmental benefits of recycling are included in the analysis. Yet other studies found the opposite result, namely that recycling is unprofitable because of the lack of high-value elements in the panels. Overcoming this economic uncertainty will be crucial to scaling PV recycling operations.
Opportunities for sustainable solar panel recycling
How can manufacturers, waste managers, governments, and other stakeholders better understand the cost and benefits of solar panel recycling? A starting point is to conduct more comprehensive techno-economic analyses (TEAs) and life cycle assessments (LCAs). These studies can share more updated cost-benefit information and account for changing commodity prices and other factors.
Recycling processes have room to improve — with more R&D, we can discover methods that recover more raw materials more efficiently than current processes. Recovering more silver, for example, can make recycling more cost effective. Projects such as Icarus may also find silicon purification breakthroughs that will reduce waste and be more efficient with raw materials for new solar panels.
Researchers can also develop innovative panel designs that account for recyclability. Planning for disassembly and material recovery in the design phase could make recycling more effective at reclaiming materials, using less energy, and creating less chemical waste.
Government policies will also have a role to play. The EU’s Waste Electrical Electronic Equipment (WEEE) regulations can be a starting point for other countries and regions. By encouraging PV recycling, governments can help spur economies of scale. As the International Renewable Energy Agency also notes, involving waste disposal partners can drive business growth and expand revenue and job opportunities, thereby developing a positive feedback loop for clean energy expansion and economic growth.