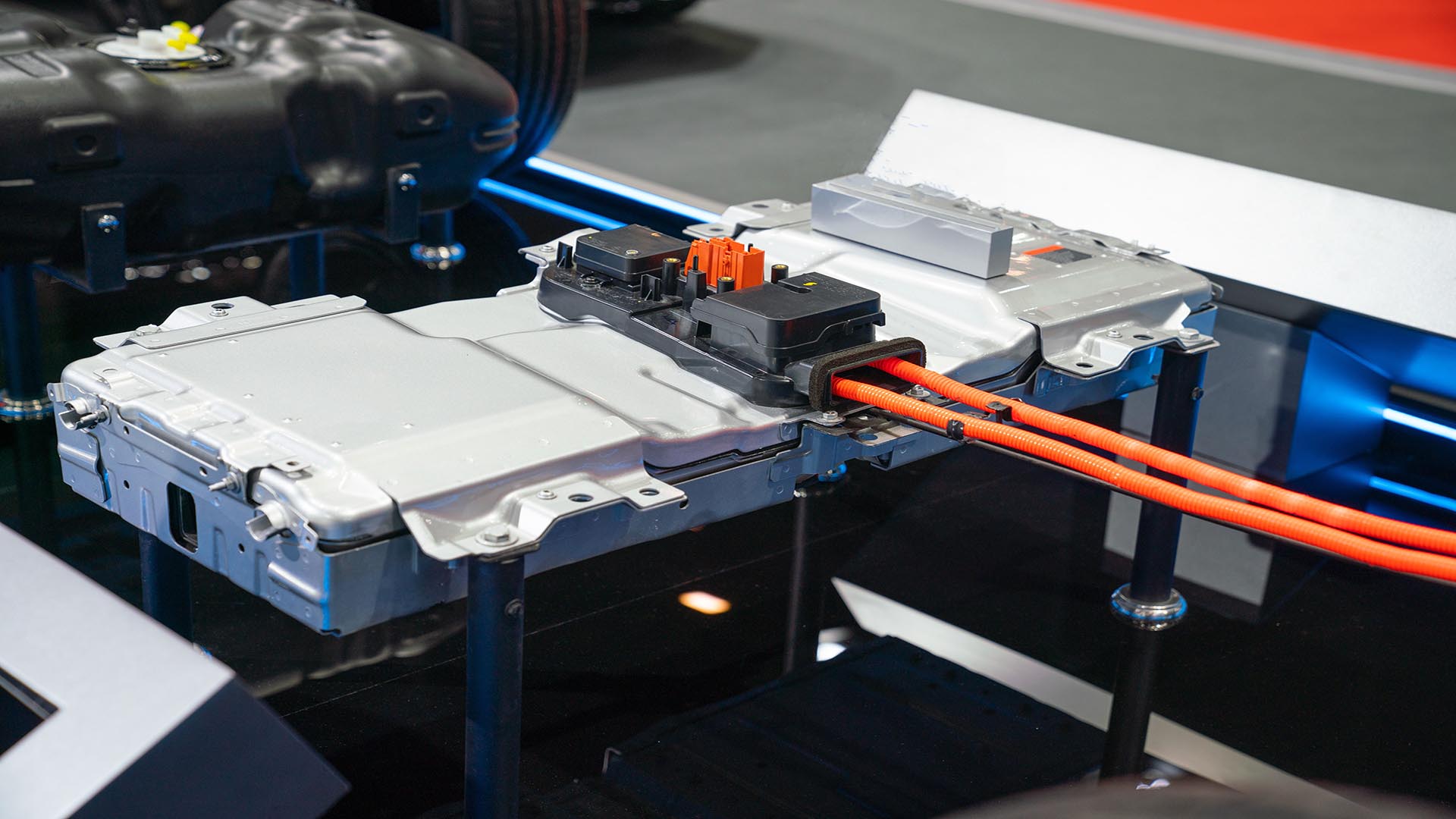
With the proliferation of electric vehicles (EVs) and electronics that rely on lithium-ion batteries (LIBs), it’s become crucial to scale up battery recycling processes. Recycling is essential to reduce waste, minimize the environmental impacts of batteries, and recover valuable materials. By implementing supportive regulations, investing in advanced technologies, and fostering collaboration, the battery recycling industry can create a circular economy that addresses resource scarcity and reduces carbon emissions.
The current landscape of lithium-ion battery recycling
The global LIB recycling industry is expanding significantly as governments and companies respond to the rising demand. As of 2025, the capacity of established recycling facilities stands at around 1.6 million tons per year. With the addition of planned facilities, this capacity is expected to surpass 3 million tons per year.
This market is primarily driven by the tightening of environmental regulations, the need for EV supply chain decarbonization, the growing number of retired batteries, and the rising demand for critical materials like lithium, cobalt, and nickel. Let’s take a closer look at these drivers:
Tightening regulations and compliance requirements
Mandatory requirements, such as extended producer responsibility (EPR), hazardous waste management, and end-of-life recycling, are shaping the industry. Well-structured recycling policies can reduce safety concerns and the loss of reusable materials from spent LIBs, while promoting the recovery of scarce resources. Additionally, circular economy policies, industry standards, and government funding incentivize growth. As seen in Figure 1, numerous policies have been developed in the U.S., EU, and Asian countries (China, South Korea, India) regarding LIB recycling over the last 10 years. Among these countries, China has been the most proactive in proposing and implementing policies that address LIB recycling.
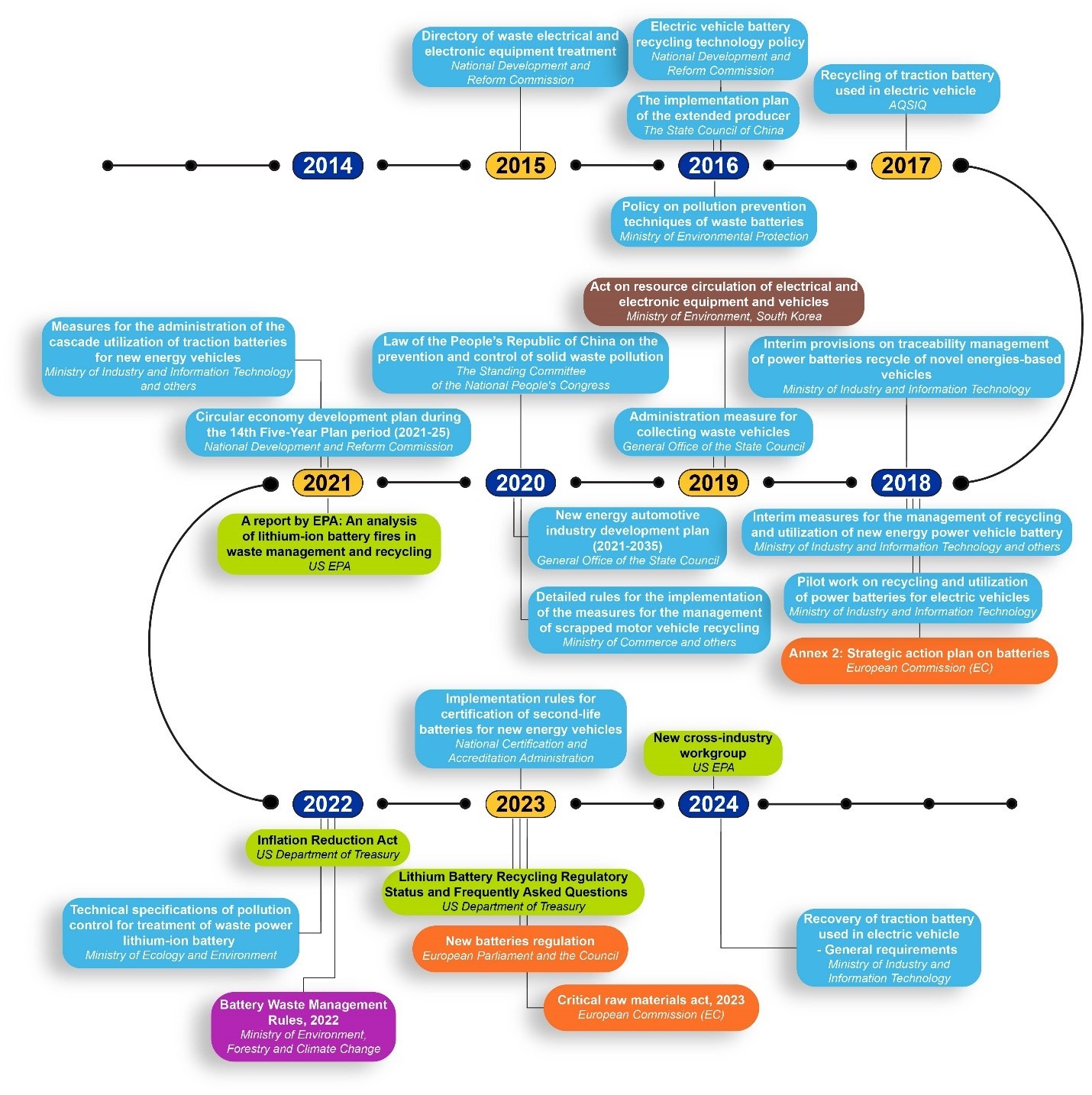
Supply-chain decarbonization is being prioritized by auto OEMs
Electric vehicles are considered clean because they don’t produce tailpipe emissions from fuel combustion. Yet, the production of their LIBs is a significant source of carbon emissions, accounting for approximately 40-60% of the total emissions from an EV’s manufacturing process. Mining and refining their necessary minerals, such as lithium, nickel, and cobalt, emits significant quantities of CO₂.
In response to increasing pressure from regulators, investors, and stakeholders for reduced carbon footprints, leading auto OEMs are seeking to reduce their emissions overall. Battery recycling and raw materials recovery are important steps toward achieving this. Additionally, battery recycling helps reduce energy consumption and carbon emissions in transportation, manufacturing, and other processes. A study by Fraunhofer IWKS estimates that recycling 1 kg of lithium batteries can reduce carbon emission by 2.7 to 4.6 kg CO₂ equivalent.
The first wave of EV batteries is reaching retirement
Simply put, more EVs on the road means more batteries in circulation. LIB performance gradually deteriorates over time, and with today’s technology, the average service life of EV batteries is five to eight years. That means the first batch of EV batteries to reach the market in previous years is now ushering in a “retirement tide.”
According to a recent study by Deloitte, the retirement scale of EV batteries is expected to grow rapidly at a CAGR of 43% from 2021 to 2030 and will reach 1483 GWh per year by 2030 (see Figure 2). The Chinese market, which leads the global EV market, is also expected to be the largest in battery recycling, occupying about 70% of the global battery recycling capacity.
With so many batteries coming out of service, it will be vital to keep these used batteries out of waste streams where they can contribute to environmental pollution. Manufacturers are also seeking to reclaim their raw materials for new batteries.
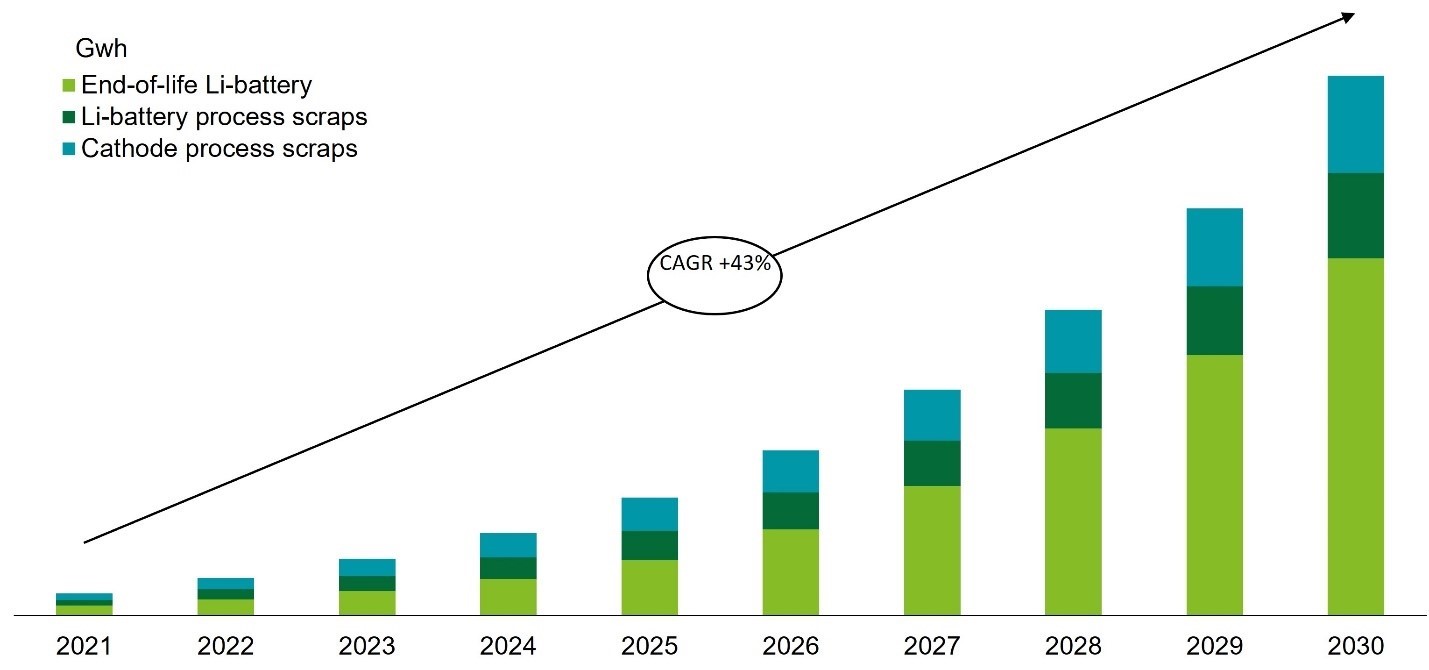
Recycling to bridge the future supply gap for critical raw materials
The development of the lithium battery industry remains constrained by the availability of upstream critical minerals. According to the IEA’s forecast, under its net zero emissions by 2050 scenario, global lithium demand will reach 1,431 kt by 2040, seven times higher than current production levels. Similarly, the demand for nickel and cobalt is expected to double by 2040, reaching 6,386 kt and 472 kt, respectively.
Despite the surge in demand for these critical minerals, expanding mining and refining capacity requires significant investment and a development cycle of up to several years. Battery recycling offers the LIB industry a pathway to reduce dependence on traditional raw material mining and mitigate risks of future supply disruptions.
Technological innovations to improve lithium-ion battery recycling
We examined the CAS Content Collection™, the largest human-curated repositories of scientific information, to better understand how battery recycling technology is evolving. Here are the key takeaways from our analysis:
Power players: Unveiling the global leaders and trends: The strong commercial interest in LIB recycling is evident from the overwhelming patent-to-journal publication ratio of 2:1, compared to the typical ratio of 1:5 (see Figure 3A). Furthermore, our analysis of the geographical distribution of total publications highlights the dominance of Asian countries in this field, as shown in Figure 3B. China has emerged as the leading player, followed by Japan and South Korea. The United States and Germany also hold prominent positions.
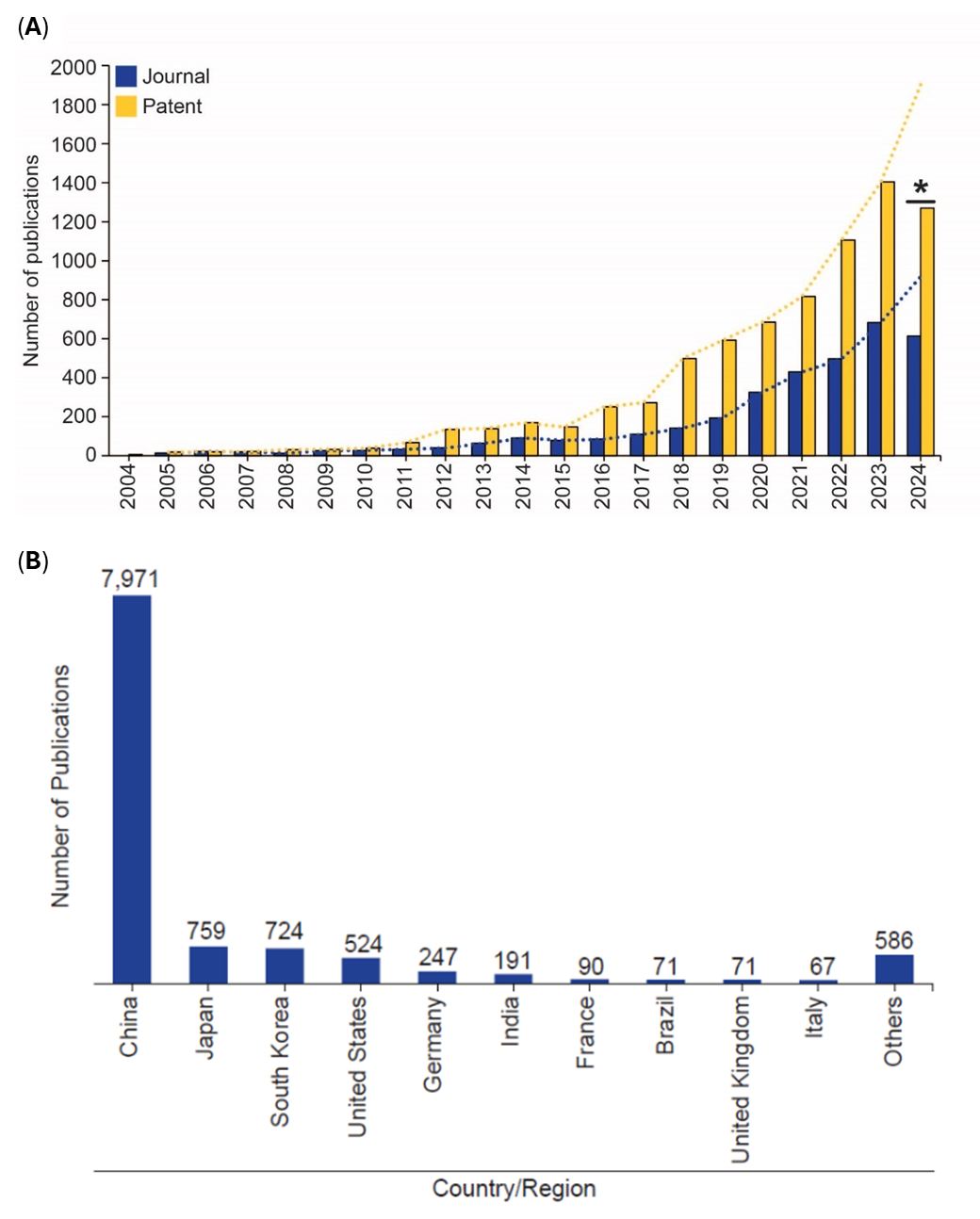
Leading the charge: Pyrometallurgy and hydrometallurgy remain dominant for LIB recycling. The primary recycling approaches for LIBs are pyrometallurgy, hydrometallurgy, and direct recycling. Pyrometallurgy relies on high-temperature treatment, hydrometallurgy uses chemical dissolution, and direct recycling aims to retain the electrode’s chemical structure. The metals recovered by these methods have varying chemical compositions, and metals recovered as alloys from pyrometallurgy often require further chemical processing, leading to hybrid approaches that combine hydro- and pyrometallurgical steps.
Figure 4 presents the publication trends in pyrometallurgy, hydrometallurgy, and direct recycling using CAS Content Collection data. The overall growth in publications underscores the increasing importance of LIB recycling, and the number of patents reflects the high commercial interest in this field. Hydrometallurgy has a slight lead over pyrometallurgy in publication volume, while direct recycling lags significantly. The higher share of journal publications in hydrometallurgy suggests ongoing fundamental research into novel, more efficient, cost-effective, and environmentally friendly chemical processes.
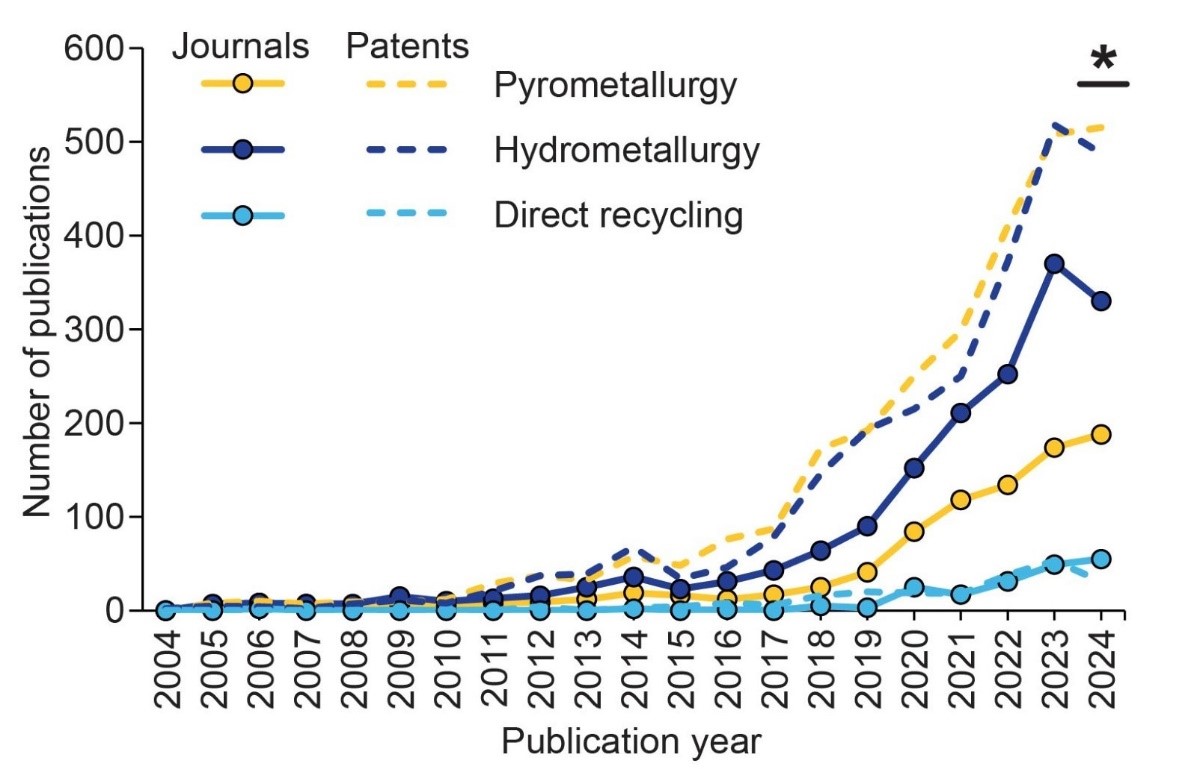
Cathode kings: The critical role of cathode recycling in lithium-ion batteries. The choice of recycling method depends on the battery components and recovered materials. The high value of metals like cobalt (Co), nickel (Ni), and lithium (Li) makes cathode recycling a top priority.
As shown in Figure 5, we analyzed the concurrence of common LIB cathode types with recycling methods. Lithium iron phosphate (LFP), lithium nickel manganese cobalt oxide (NMC), and lithium nickel cobalt aluminum oxide (NCA) are three major cathode types associated with EVs. Among them, LFP and NMC are widely adopted, and their recycling methods are broadly discussed in the literature, with a general prevalence of hydrometallurgy, pyrometallurgy, hybrid, then direct recycling. LFP has slightly more publications on pyrometallurgy, most likely due to its low-value metals making hydrometallurgy’s chemical requirements less cost-effective.
NCA is relatively less used, so its recycling is studied less in the literature. Lithium manganese oxide (LMO) is a type of cathode used in hybrid automobiles or electronics, whereas lithium cobalt oxide (LCO) is used in electronic devices. The publication prevalence of recycling these cathodes also followed the general trends mentioned above.
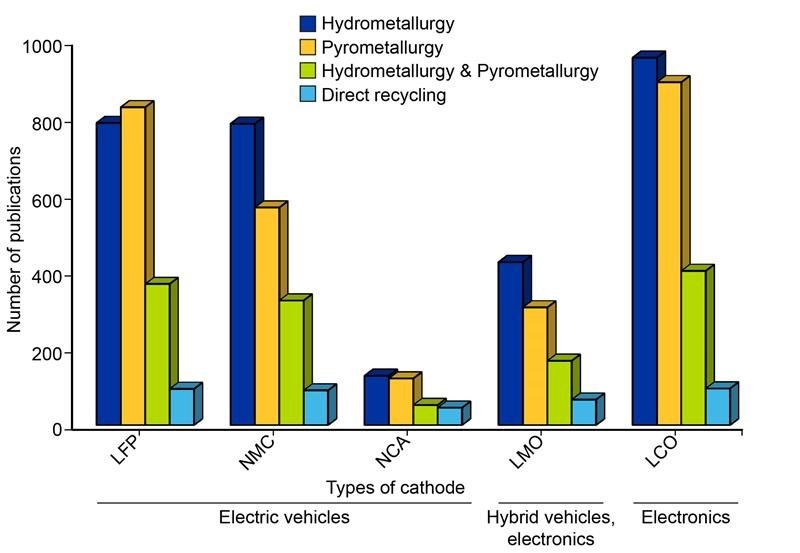
Recycling showdown: The ultimate comparison of lithium-ion battery recycling methods. A comparison of pyrometallurgy, hydrometallurgy, and direct recycling reveals that each method has distinct advantages and drawbacks (see Figure 6). Pyrometallurgy is energy-intensive, needing substantial electricity or fuel to reach necessary temperatures, and it generates extensive emissions. This process also struggles with recovering lithium, aluminum, and manganese, often forming a slag needing further processing.
Hydrometallurgy, while less energy-intensive, produces considerable liquid waste requiring additional treatment. Direct recycling and hydrometallurgy may require customization based on cathode type, but pyrometallurgy’s high-temperature approach can process diverse battery types effectively. Ultimately, no method is “perfect” from an environmental or material recovery standpoint, but each has a role in improving the circularity of battery production.
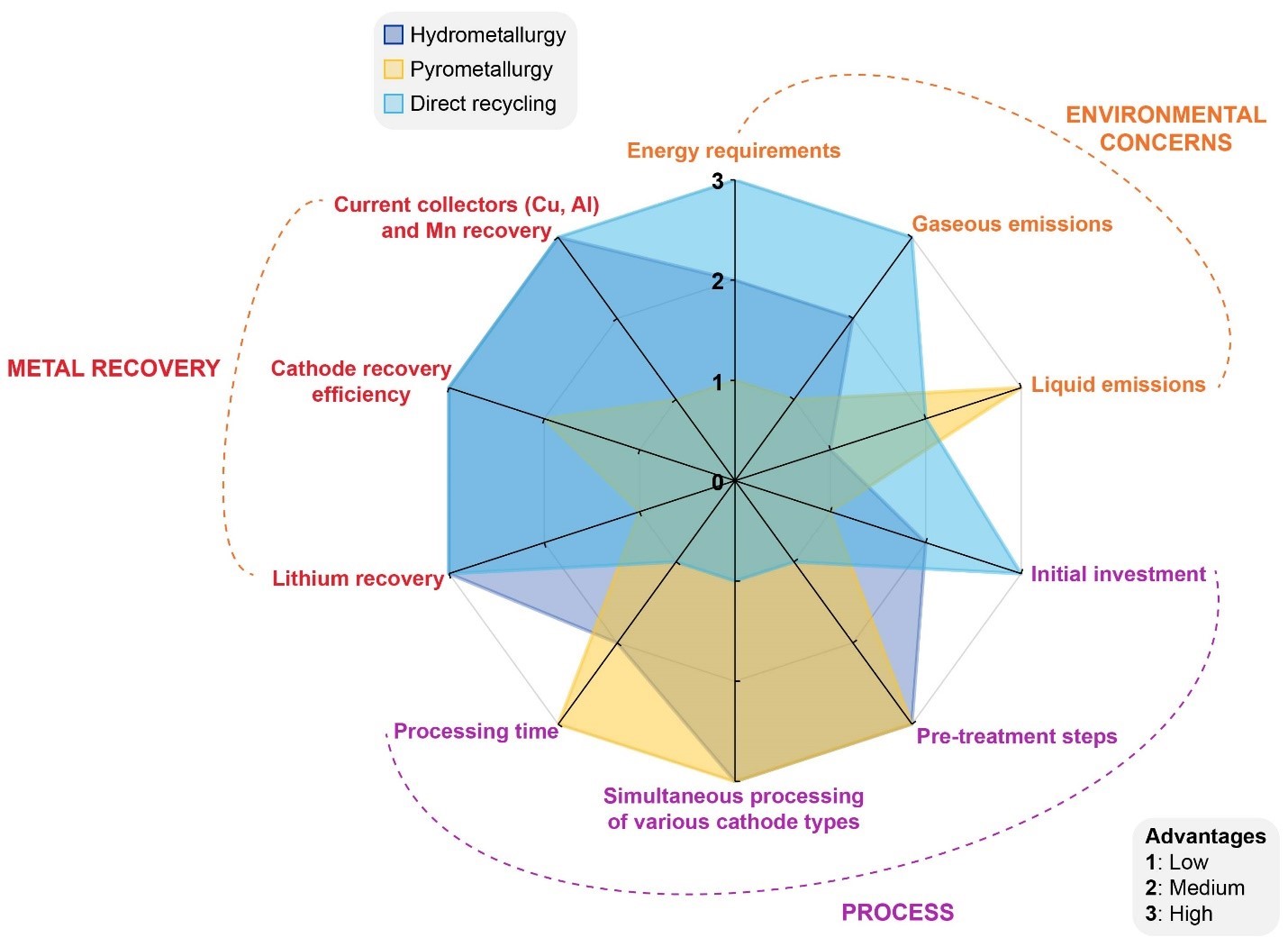
Future directions to expand recycling
Although the battery recycling industry faces challenges such as high costs, complex recovery processes, and fragmented collection and logistics, the future is still promising thanks to the long-term trends driving interest. Advancements in technology, digital applications, and increased industry collaboration are set to revolutionize the landscape, making battery recycling more efficient and economically viable.
- Recycling technology innovations to tap the cost and safety issues
Battery recycling poses several complex challenges, ranging from operational inefficiencies and safety risks to regulatory compliance and environmental impacts. One of the major issues is the wide range of different and evolving battery formats, designs, compositions, and chemistries, which complicates the recycling process and requires specialized techniques. This complexity, along with the presence of toxic and flammable substances, often makes the recycling process energy-intensive and requires costly safety measures.
Government funding for battery recycling is an important tool to tackle these challenges. Recycling technology innovation and emerging technologies focus on improving metal recovery rates, making recycling processes economically viable and sustainable. For instance, direct recycling aims to retain the functional structures and chemical compositions of the materials to reduce the energy and environmental costs. Moreover, novel and promising methodologies such as deep eutectic solvent (DES) and microbe-based leaching are at the early stages of development. These technologies can reach maturity and overcome persistent cost and safety challenges with funding and support.
- Adoption of digital tools to increase traceability and efficiency
Manual processes often lead to low material recovery rates, high costs, and potential safety hazards. Additionally, regulatory pressures require meeting strict standards for recycled content and environmental impacts. How can digital tools help? They can be applied for tracking materials throughout the battery lifecycle, automating the sorting and disassembling of battery components, and optimizing the recycling schedule. For instance, cloud-based platforms and blockchain technologies allow companies to track and trace the lifecycle of materials from collection to recycling and reintegration into the supply chain. This process ensures compliance with environmental regulations and helps stakeholders monitor key metrics, such as material recovery rate and carbon emissions.
- Collaboration across the value chain to scale up recycling
The fragmented supply chain of battery recycling has been one of the most critical barriers to scaling up the industry. In China, only 25% of retired EV batteries are recycled through formal channels, leaving recycling companies with limited control over feedstock quantity and quality. This lack of consistency hinders their ability to scale operations effectively.
A key component to addressing this issue is the development of batteries designed to be recycled. These new developments make the disassembly process more efficient and sustainable. As a result, materials suppliers, EV producers, auto brands, and recycling companies are collaborating more frequently. By pooling their expertise, these stakeholders can address challenges and adapt to industry shifts faster.
- Strategic pathways to profitability in battery recycling
Battery recycling profitability depends on three key factors: recycling costs, the value of recovered materials, and environmental benefits. Variables such as transportation distances, labor costs, pack designs, battery chemistries, and the choice of recycling technology influence recycling costs. To achieve financial viability, recyclers must focus on cost reduction through automation, minimizing transportation expenses, and adopting the most effective recycling methods tailored to the value of recovered materials.
As stakeholders invest in smarter solutions, we can expect a new era of sustainable battery management that supports the growing demand for electric vehicles, paving the way for a greener circular economy. LIB recycling faces numerous hurdles, but it also stands to benefit from technological advances. Industry collaboration and government support will also be critical, and as the economic and environmental benefits of LIB recycling grow, so will the industry. The innovations happening today are building a smarter, more efficient recycling chain and paving the way for a sustainable, circular economy in the battery and EV sectors.
For more information on lithium-ion battery recycling, see the recent joint report from CAS and Deloitte